Unlocking the Three Secrets of Co-Extrusion Feed block
2023.12.29
In
the extrusion process, co-extrusion is a widely employed technique that
cleverly combines two or more different plastics to form multi-layered plastic
sheets or films. The primary purpose of using this technique is to combine the
characteristics of various plastics, enhancing physical and mechanical
properties, as well as meeting specific product requirements such as
transparency, temperature resistance, or cost reduction.
There
are two main methods of co-extrusion : using multi manifold dies and the
well-known combination of feed block with extrusion die . The differences
between these two methods are as below:
Multi manifold extrusion die |
Feed block with Extrusion dies |
|
Number of Layers |
2-5 layers |
2-11 layers |
Applicable Plastics |
Temperature difference of 20 degrees or more |
Plastics with similar temperatures |
Operation Method |
Different plastics directly enter separate mold cavities and combine in the mold forming area |
Different plastics enter the layering device, combine within the layering device before entering the mold |
Co-extrusion
in two ways: (Left) Multi manifold extrusion dies, (Right) Feed block with
extrusion dies
The
feedblock plays a crucial role in co-extrusion and its operation can be
summarized in three letters: DCA
D: Division
The
feed block is designed based on the placement and quantity of the
extruders, allowing for various inlet sizes and positions. The internal
channels of the feed block are designed according to the structure and
proportions of the product, ensuring that different plastics can enter and
stack in the feed block based on the set ratios. For example, a two-layer
structure implies two internal channels, a three-layer structure has three
channels, and so on.
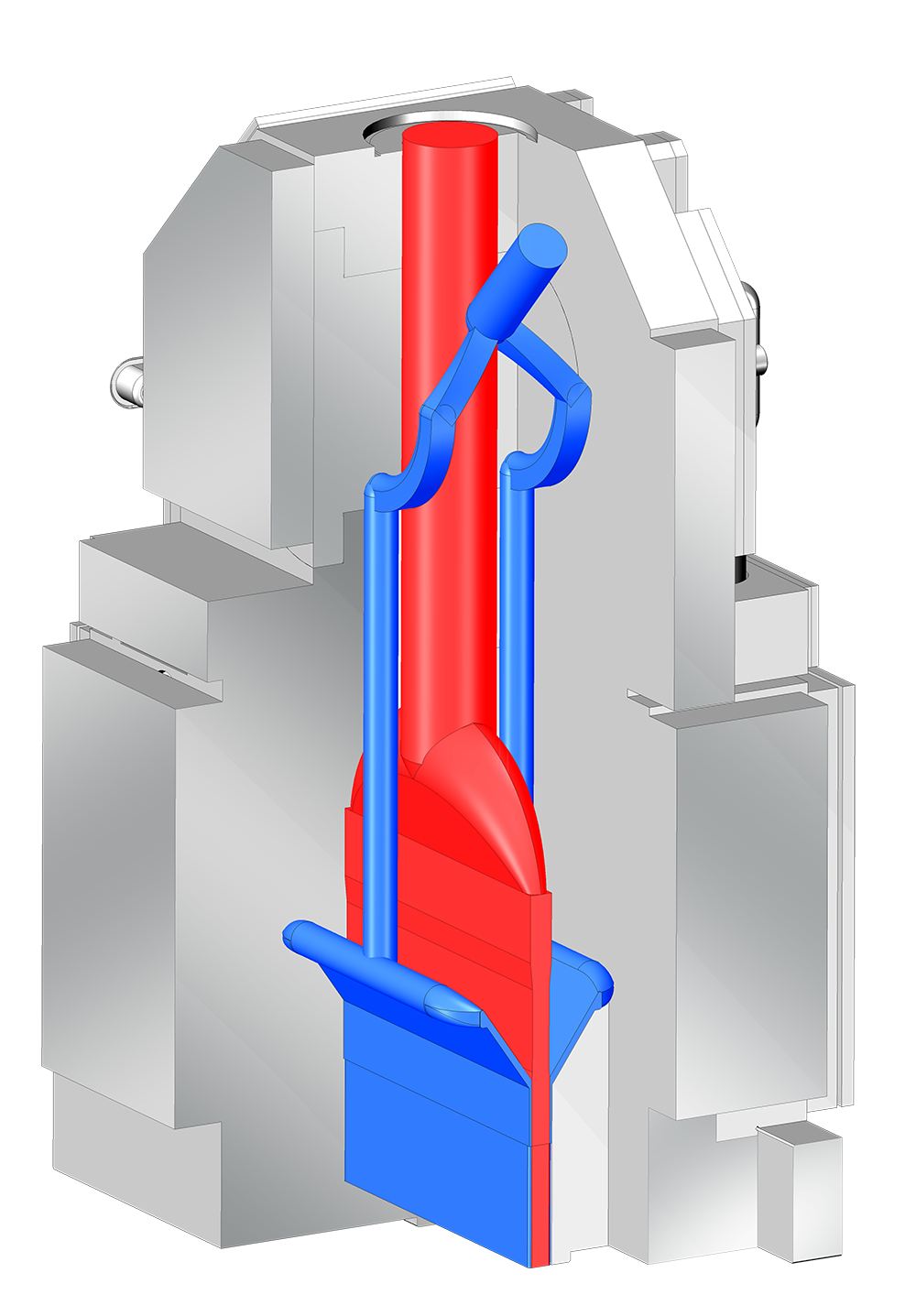
inlets
and channels in the feed block designed based on the extruder and product
structure.
C:Combination
A:
Adjustment
The feed block features two adjustment tools to facilitate achieving optimal layering effects. The most commonly used tool is the adjustment lever, used to finely tune layering proportions. It functions like a flow valve, altering the flow rate in the internal channels. For instance, it can adjust the material ratio from 15% to 10% for a single layer.
Another
tool, the distribution pin, is used in specific situations to optimize
interfaces in each layer. In cases where uneven layer interfaces occur despite
uniform product thickness, the distribution pin allows for minor adjustments.
In
addition, to accommodate various changes in product structure, the feed block
can be used in conjunction with a selector to alter the direction of the
internal flow paths, offering several different structural variations. This
allows for product diversification in the simplest manner. For example, a
two-extruder, two-layer structure (AB) can be transformed into a two-extruder,
three-layer (ABA) structure by using a selector.
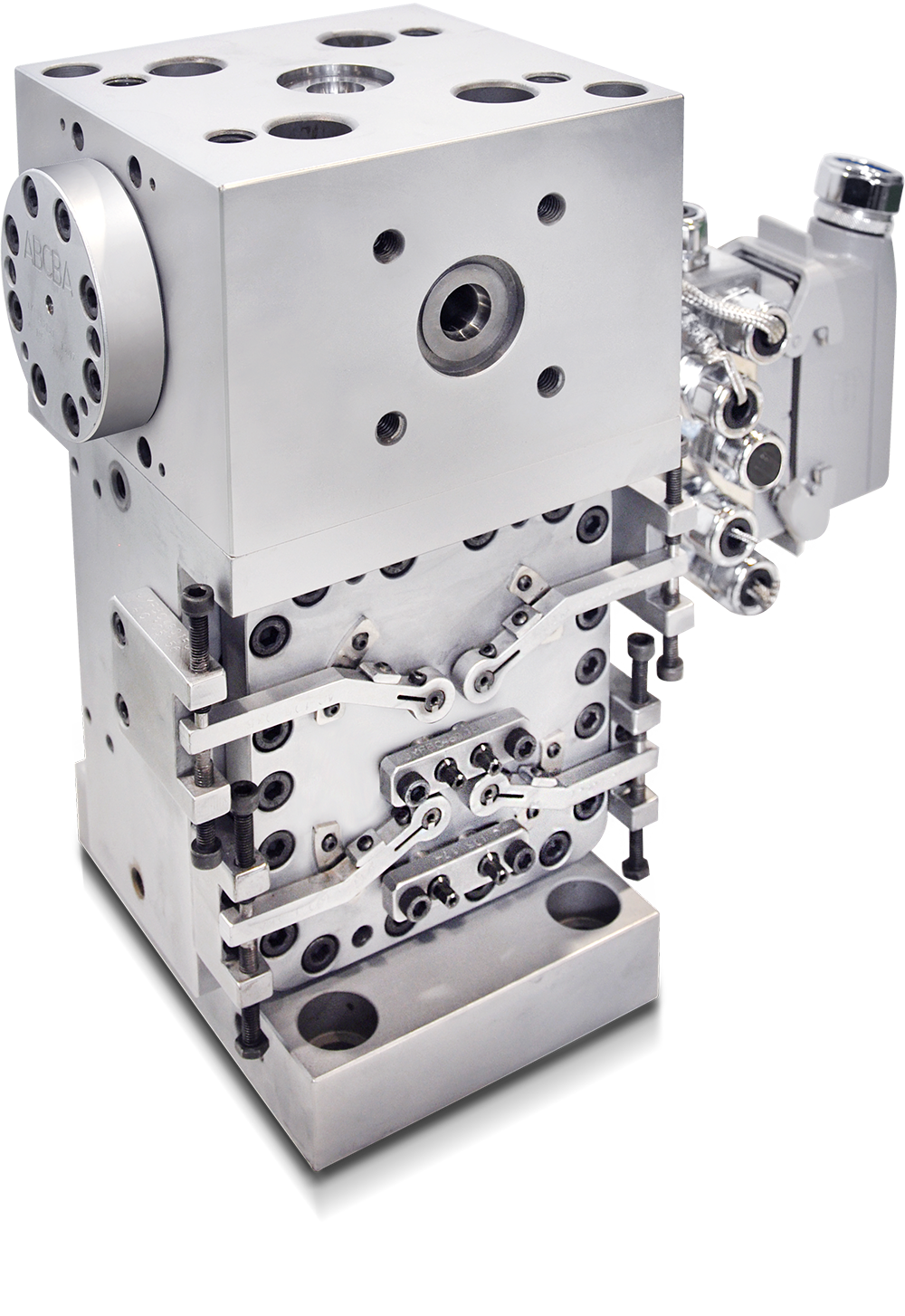
The
feed block includes different adjustment tools for fine-tuning layering
proportions.
The
feed block, playing a crucial role in the co-extrusion process, allows for the
optimization of layering quality through meticulous adjustments. Whether using
a feed block with extrusion die or multi- manifold extrusion dies, adept use of
co-extrusion technology provides a flexible and effective solution for the
development and production of plastic products.